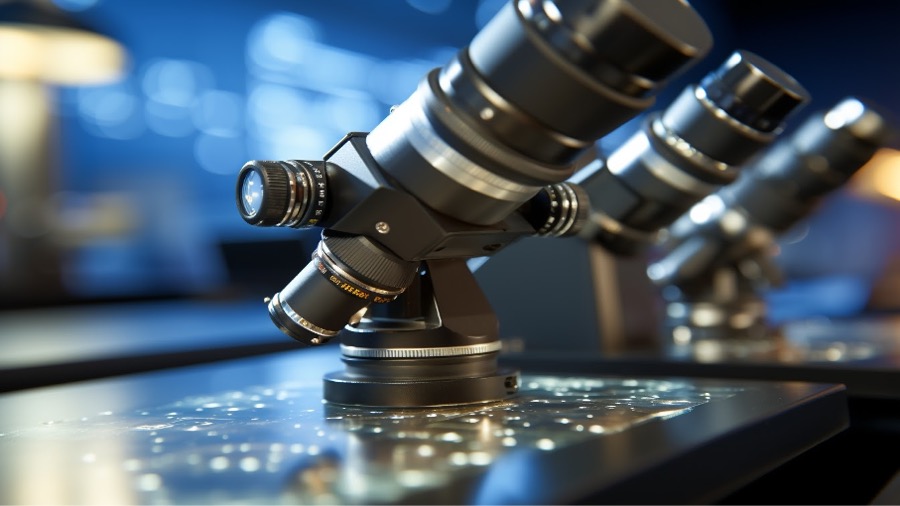
8D-问题分析与解决技术【2天】
中小型企业的80%的基础管理工作都应该谁去落实?80%的效率提升都应该谁去推动?80%的粗制滥造小事件都每天发生在谁身边?是谁每天从早到晚始终目不转睛盯着现场?是谁每天从早到晚严守把控作业安全、产品缺陷、设备保养、进度督导、规范作业的执行监督?又是谁第一个愿意与员工在失败中共同学习与成长?企业引入了不同类型的西方式管理理论、各种管理体系认证的洗礼,为什么公司还是找不到更好的经营质量管理的策略与方法?上有政策,下有对策,为什么企业家的想法总是不能让员工上下一致的理解与认同?谈质量文化,为什么部份企业总是不停的在重复思想与行为的“两张皮”现象!
课程收益:
1) 熟练掌控团队的问题解决方法,解决潜在风险的生产线质量问题;
2) 掌握问题解决过程的八个步骤(8D)及其底层逻辑;
3) 熟练应用团队解决问题过程中所需的基础性工具,培养解决问题的能力
第一讲:8D问题分析与应用技术
1) 8D问题分析与应用技术地图
2) 什么是8D
3) 企业为什么要推行8D
4) 什么时候使用8D
5) G8D适用范围与目标
6) D0 准备G8D
7) D1 建立小组
8) D2 描述问题
9) D3 制定并实施ICAs(临时措施)
10) D4 定义、验证根本原因和问题逃出点
11) D5 选择和验证PCAs(永久措施)
12) D6 实施和确认PCAs(永久措施)
13) D7 防止问题再发生
14) D8 表彰小组和个人的贡献
15) G8D 改善案例
第二讲:问题分析与聚焦技术
1) 问题解决流程PSP的定义与目标
2) 5-Why现场问题分析法
3) 思维导图与问题分析的整合技术
4) 如何让员工从失败的案例中成长
5) 建立自动自发解决问题的氛围
6) 如何强化全员工简易工具的应用
7) 避免解决方案与执行形成的“烂尾楼”
8) 化解团队管理的冲突及油条式员工
9) 站在金钱的视角看问题的本质
10) 如何将简易品管工具生活化与效益化
案例:问题思考-黄豆油滤油机的故事
第三讲:营造全员持续改进的氛围
1) 突破现场管理困局的思维
2) 奉行“不、没、难”主义
3) 提升员工意识三道防火墙
4) 公司的利润是管理出来的?
5) 现场浪费与持续改进系统的整合
6) 产品成本模型-标准成本构成
7) 团队绩效优化的三个方向
8) 品质成本结构及计算表
9) 削减现场成本的十步骤
10) 持续改进的基本方向与策略
11) 提案技术的三大支柱
12) 案例:现场改善的标杆成果